Featured Instrumentation Articles
- Chemical Instrumentation Case Studies and Articles-Endress+Hauser
- Life Science Instrumentation Case Studies and Articles - Endress+Hauser
- Electric Heat Tracing – A Comprehensive Guide
- Water & Wastewater Treatment Instrumentation Case Studies-Endress+Hauser
- Food Processing and Beverage Instrumentation Case Studies-Endress+Hauser
- Pulp and Paper Manufacturing Process Improvements
- Watlow Industry 4.0 Resources Downloads
- Watlow Process Data Controller Resources Downloads
- Watlow Process Heating Resources Downloads
- Case Study - Chemical Plant saves 200K with Endress+Hauser Memograph
- Endress+Hauser Shows How Production Data can Increase Efficiency and Output
-
Should I Use Diaphragm Seals or Isolation Rings to Protect Plant Instrumentation from Harsh Process Fluid?
- Endress+Hauser Feature: Micropilot Radar Level Measurement
- Reduce Energy Use with Industrial Process System Energy Savings Audits
- Endress+Hauser Featured Downloads – Q4 2022
- Armstrong Food & Beverage Products & Services
- Endress+Hauser Instrumentation Meet Food & Beverage Demands for Stringent Measurement
- Prevent Dust Explosions at your Plant
- Water/Wastewater Systems Problems Guide
- What are the Four Classic Energy Measurements in Water (Head) ?
- How to Know Why and When do your Flowmeters need Calibration?
Should I Use Diaphragm Seals or Isolation Rings to Protect Plant Instrumentation from Harsh Process Fluid?
Diaphragm seals and isolation rings are integral to safe and efficient operation in tough environments like chemical plants, water treatment plants and mining and mining facilities. All kinds of applications use diaphragm seals and isolation rings to protect sensitive instrumentation from the damaging effects of harsh process fluids.
What Is a Diaphragm Seal?
A diaphragm seal is a device installed between the process fluid and one or more instruments. A thin, flexible membrane called a diaphragm isolates an instrument or instruments from the process fluid, creating a leak-tight and corrosion-resistant seal
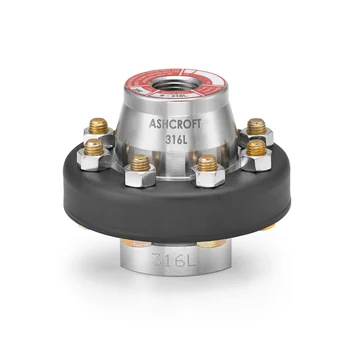
What Is an Isolation Ring?
An isolation ring is another type of isolator with a ring-like design that forms a protective barrier between pressure measuring instruments and process flow. Isolation rings are used to prevent harsh process fluid from damaging pressure gauges, switches, high-priced transmitters, and other instruments.

When to Use a Diaphragm Seal vs an Isolation Ring
Since both devices are isolators, many people wonder when to use a diaphragm seal vs an isolation ring. In general, diaphragm seals are primarily be used when there are corrosion concerns, and isolation rings are used to prevent clogging.
In our experience at Carotek, the best solution depends on a combination of factors including:
- the installation
- size and concentration of particulates
- fluid composition
- conditions like system pressure and temperature
Cost also needs to be considered. Diaphragm seals typically cost less than isolation rings, so it may be possible to reduce cost by using a diaphragm seal vs an isolation ring in cases where either would be suitable.
When to Use a Diaphragm Seal
The size of the solid particulates makes a difference. If the fluid contains a low percentage of solids and the particle size is similar to sand particles, a diaphragm seal may be a good solution.
Diaphragm seals are often added as isolators for two main reasons:
- applications that involve harsh, corrosive chemicals
- fluids with small amounts of particulates that threaten to clog the instrument assembly’s sensing element
Clogging is the main reason that a diaphragm seal may not be ideal for a given application. It’s also important to consider whether flushing the inside of the lower housing of the seal would be too labor intensive. Certain diaphragm seal designs are less prone to clogging, including:
- inline diaphragm seals
- saddle seals
- flanged seals with an extended diaphragm
In addition, some seals are designed with a flushing port to flush material and avoid clogging. However, if the particulate is too rough or abrasive, the metallic diaphragm can be damaged.
When to Use an Isolation Ring
For sludges and slurries that would otherwise clog the cavities of a diaphragm seal, isolation seals offer an alternative solution.
Isolation rings are much better suited to deal with abrasive particulate in a process than diaphragm seals are, although they operate in much the same way. Some isolation rings are designed with sensing elements (a.k.a. liners or bladders) that can withstand the continuous impact of particulate pushing through the piping, such as more chemically resistant PTFE or more durable natural rubber or Buna.
There are a few things to keep in mind when considering an isolation ring for a given application.
- Installation: Isolation rings range in size from ½-inch to 36+ inches. Larger isolation rings can be tricky to install.
- Cost: The larger the isolation ring, the more expensive to repair or replace down the line.
- Repair: Repairing an isolation ring means properly cleaning and sanitizing it, sending it for recalibration, refilling system fluid, and any other maintenance.
- Removal: Removing an isolation ring is not simple. In general, it’s necessary to shut down the process while the piping is cleaned and the flange is dismantled.
ASHCROFT ISOLATION RINGS are designed with a Safe Quick Release feature to make it a little easier to remove the instrument. A dry break coupling allows the instrument to be removed without losing fill fluid
Carotek Isolator Recommendations
At Carotek, our Instrumentation and Municipal Groups both use diaphragm seals and isolation rings in conjunction with pressure gauge instruments to design engineered assemblies geared for specific applications.
Carotek specialists can help you decide whether an isolation ring or diaphragm seal will function better to protect plant instrumentation by looking at your entire application.
- If process compatibility is required, we may recommend an Ashcroft 201 threaded diaphragm seal since the diaphragm material in this style isolator is available in a large variety of options suited to harsh process fluids.
- For applications where corrosion resistance is less important, an Ashcroft 82 threaded isolation ring would be an economical way to avoid clogging. It is designed for threaded piping systems to eliminate process accumulation for more accurate readings.
CONTACT our industry experts at Carotek for assistance finding the best solution to protect plant instrumentation.