Flowserve Valve Solutions for the Global Brewing Industry
Beer, one of the oldest beverages produced by man, is brewed in production facilities around the globe. In North America, the brewery market has had some ‘disruptive change’ in the last decade with the explosion of smaller craft beers currently preferred by many younger Americans. As a result, many larger brewery companies have closed older larger breweries and purchased smaller craft competitors.
The modern brewing industry is a thriving worldwide business, centered around:
- several dominant multinational companies
- many thousands of smaller microbreweries (smaller than 15 000 USbeer barrels)
- nano-breweries
- regional breweries
Global production in 2015 totaled greater than 51 billion U.S. gallons.
With steep and challenging competition in the brewing market, it’s important that valve suppliers can offer quick distribution, responsive service, and competitive prices. Flowserve’s food and beverage capabilities offer a distinct advantage in supplying control and manual valves for brewing industry process equipment.
Advantages of Flowserve Valves for the Brewing Industry
Flowserve valves offer several advantages for the brewing industry.
- Flowserve valves are manufactured to the most rigorous quality standards to provide reliable products.
- Flowserve’s unparalleled depth of engineering experience in the food and beverage industry ensures optimized product and material selection and reliable operation.
- Flowserve has been a key player since the beer brewing process was commercialized on a large scale. Lessons learned have been built into today’s valves, increasing reliability, maintainability and product life.
Quick Look at Flowserve Valves for the Brewing Industry
Throughout the brewing process, many types of valves are commonly used to regulate the flow of fluids through process pipes in the plant.
- Manual Plug Valves. The simplest type of valve used in brewing is the manual plug valve, a plug with a hole that can be turned to either restrict flow or stop it. A plug valve is easily recognizable, and sometimes has a handle that turns 90 degrees from fully open to fully closed.
- Diaphragm Valves. In a diaphragm valve, a soft diaphragm is pushed against a bell-shaped feature using a mechanical screw. The diaphragm mechanism allows liquid or gas flow to be controlled within the valve’s total variability, but the flow pressure tolerances are fairly tight.
- Butterfly Valves. Due to its compact design and wide pressure and flow tolerances, the butterfly valve is the next most commonly used valve in breweries. It consists of a metal disc that rotates within the body of the valve and closes against a rubber seal. Its flow-through design makes it easy to clean.
- Manifold Valves. The fourth type of valve used in brewing is a manifold valve, often used in large breweries where systems are hard-piped. This is a complex valve that can be installed either vertically and crossed with horizontal piping, and is common in release matrixes. Although it s a very useful type of valve, it tends to be very costly.
Flowserve Valve Products and Capabilities in the Brewing Process
Beer brewing is a universal process all around the world, with light variations in between the processes. In general, there are several steps involved in the brewing process that can be broadly classified into three main areas. Valves are used in all three:
- Brewing – includes malting, milling and mashing. These initial processes are the toughest applications in the brewery and the most regulated for final product.
- Fermentation – includes lautering, boiling, fermenting, conditioning and filtering.
- Packaging -- putting the beer into the containers in which it will leave the brewery. This process typically means putting the beer into bottles, which are filled in the bottle filling machine.
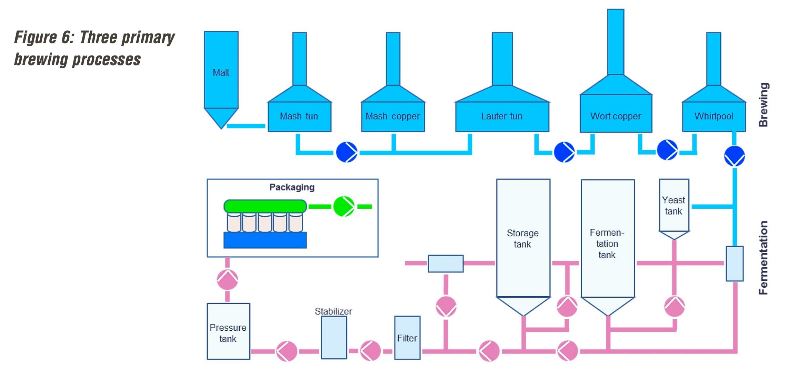
Most Commonly Used Valves in the Brewing Process
In addition, there are application areas for three-way and bottom-drain flow valves within the brewing process. “Food-safe” grade requires high-purity and aseptic process performance valves.
The following are typical Flowserve valves used in different brewery processes, including critical and general services applications.
Control valves
Valtek FlowTop/GSV (Globe)
- High capacity
- High performance
- Ease of maintenance
Valtek Mark One (Globe)
- Heavy top guiding
- High performance
- Severe service trim available (Noise reduction trim, Anti-cavitation trim)
- VL Series actuator (Field reversible, Double-acting spring return)
Valtek Mark One (Mixing/Diverting)
- Highest rated Cv
- Precise control
- Reliable shut-off
Kammer Aseptic
- Different surface finish – 0.4 to 0.6 μm
- Bellows option
- Standard – without dead lag
- Ultra-clean aseptic version
Kammer Tank Bottom Valve (Globe)
- Seal-welded standard construction
- Seat ring designed to fit tank outlet dimensions
- Compact and lightweight
- Different outlet angle
Valtek MaxFlo 4 (Eccentric Plug)
- Seat design options
- Stuffing box packing options
- Primary steam seal plus two optional secondary seals provide triple-leak protection
- Wide range of optional materials includes: D20, DMM, DC2, DC3, DNI and DNIC
- Exceeds shut-off requirements of ASME/FCI 70-2 for all classes
Valtek Valdisk (Butterfly)
- Jam-lever toggle soft seat
- Single pivot point for actuator to disc connection
- Self-centering seal
- Non-selective disc and shaft for cost reduction
Valtek and NAF (Segmented Ball)
- Highest capability and rangeability
- Abrasive, erosive and corrosive fluid
- Slurry, two-phase flow
NAX Torex Butterfly Valve
- Seat design options
- Stuffing box packing options
- Primary steam seal plus two optional secondary seals provide triple-leak protection
- Wide range of optional materials includes: D20, DMM, DC2, DC3, DNI and DNIC
- Exceeds shut-off requirements of ASME/FCI 70-2 for all classes
Flowserve Butterfly Valve (Butterfly)
- Integral bi-directional travel stop
- Field-reversible action (180 degrees)
- Concentric nested spring design
- Broad size range for optimum actuator sizing
- Internationally accepted mounting standard (ISO 5211/Namur VDI/VDE 3845)
- Exceeds shut-off requirements of ASME/FCI 70-2 for all classes
Summary
With the advent of craft beers and micro-breweries, the reach of the brewing industry is even further across all strata of the global population. With this large following, the beer brewing market will continue to grow amid changing conditions such as the green environment necessitating some approaches to industry and/or beer brewing.
New market developments will help energize the beer brewing industry as we move into the future, but conventional beer brewing methods will largely remain the same, requiring the same processes and equipment, supported by reliable and long-lasting valves manufactured by Flowserve for the food and beverage industry.
*All information sourced from Flowserve