Pump downtime is costly. Reviewing pump system reliability can improve plant productivity by reducing the frequency of outage, cost of repairs, and cost of lost production. An effective pump reliability program can also improve morale and safety. Creating an ongoing program is often simpler than it may seem. This was originally published in Pumps and Systems Magazine - January 2018.
A First Class Pump Reliability Program Simplified
Reviewing pump system reliability can improve profitability by reducing the frequency of outage, cost of repairs, and cost of lost production. An effective pump reliability program can also improve morale and safety. Creating an ongoing program can be made simpler with the right steps.
Find the Right Pumps for the NPSH
When implementing a pump reliability program, you will need an inventory of all pumps in facility, as well as TDH – total dynamic head calculations for the application each pump operates in (either on its own or within a pump system). Each pump should be evaluated to make sure it is appropriate for the flow, TDH and suction pressure where it is used. This article’s focus is on NPSH.
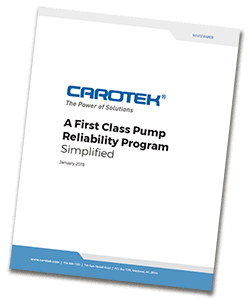
NPSH (Net Positive Suction Head)measures absolute pressure in a liquid for the suction end of a pump application.
NPSHr (Net Positive Suction Head Required) measures NPSH required for the pump. For any given application, a certain NPSH is required or optimal (NPSHr) to avoid cavitation damage or reduction in pumping. Pump manufacturers supply a pump curve for any pump in your facility that indicates the NPSHr for the pump at a given capacity.
NPSHa (Net Positive Suction Head Available) measures NPSH available at the pump inlet. Technically, NPSHa provides “a measure of the pressure that stands between the liquid in its current state and the formation of vapor bubbles (boiling).” 1The NPSH available to a given pump is a function of atmospheric pressure, temperature, supply elevation, and the dynamics of pumping.
When determining the NPSHa for a given pump, usually you use the “worst case scenario,” because the variables can be affected by rates of flow and weather conditions. NPSHa is roughly:
NPSHa = Atmospheric pressure (converted to head) + static head + surface pressure head - vapor pressure of your product - loss in the piping, valves, and fittings2
When selecting a pump, the NPSHr requirements of the pump need to be compatible with the NPSHa made available by the system in which the pump is installed.
- A pump with excessive NPSHr requirements will operate inefficiently if the NPSHa is lower than the NPSHr of the pump.
- A pump that requires more NPSH than the system has available will never operate properly, and is likely to suffer internal damage rather quickly.
To make sure you have the right pump for your system’s NPSHa, you usually want to factor in suction conditions and the variability of NPSHa under the potential range of operating conditions.
Identify Bad Actors
To improve overall pump reliability, and to increase a plant’s Mean Time Between Failure (MTBF), it is important to identify bad actors. You first need to define what “bad actors” means for your operation. Pumps that spend more time in repair than in service can obviously be called bad actors before any data is even collected. Beyond that, bad actors can be defined by some combination of repair cost and failure rate3, usually within acceptable reliability limits determined by management. For example, any pump that fails more than 3 times/year or requires more than $20,000 in repair costs in a 12-month period may be considered a bad actor.
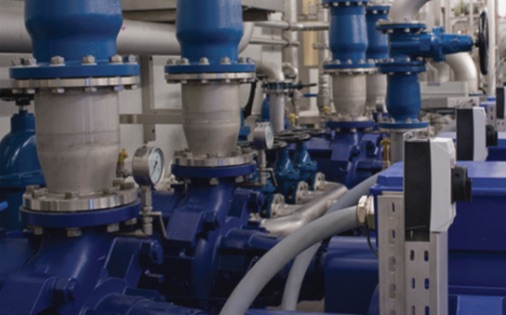
Make sure your NPSHa meets your NPSHr.
Putting together a maintenance reliability program to weed out the bad actors usually requires a team effort. Often the team includes a combination of engineers, a management sponsor, operators,maintenance technicians and a pump vendor representative. The pump vendor rep should offer supplies and services including warehousing spares, a maintained site pump database, and assistance with new application and upgrade projects.
Some of these members may rotate, and the management member may or may not attend meetings.
Ideally you’ll have a complete inventory of your facility’s pumps, pump curves, and parts lists on hand. To identify which pumps should be considered bad actors consider the following:
- Start with a list of the MTBF numbers. Focus on pumps that fall on the low end of the MTBF, such as the bottom 25 percent. Also consider adding to the list any pumps that see few hours of operation, but still fail frequently.
- Estimate the cost of production loss for each of the pumps in question.
- Create charts showing frequency of outage, cost of repairs, and production loss.
- Determine which equipment tag numbers are the worst performers that need to be addressed
By doing this exercise and displaying the results on a series of charts, it should be possible to see whether there is a problem with a specific pump, for example. Further investigation, such as vibration studies or field measurements of flows, can help determine the root cause of failures. Vendor representatives can help.
Implement Remediation
To continuously improve reliability, periodically perform remediation and make sure the pump maintenance management data remains accurate. That means making sure all your pump data is up to date and reflects current conditions. By performing remediations, you can expect to:
- Increase equipment data accuracy for decision making.
- Increase maintenance efficiency.
- Reduce total operating costs.
- Reduce operating risk.
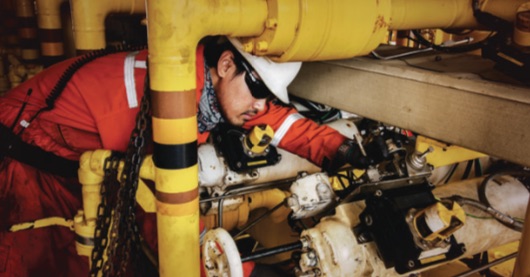
The steps to conduct a thorough pump system remediation effort usually include the following:
- Physically inspect and verify all system component information.
- Verify system drawings.
- Review analysis of system.
- Update spare parts information sheets, which may become outdated as part numbers are superseded.
- Update maintenance spreadsheets or database.
The data collected should include the model number, asset details (name/location), and serial number of all pumps. It should also include detailed pump and parts lists. And finally, a list of pump part numbers, types, number of pumps using that part, and a stock list is useful.
Some distributors and vendor representatives have site survey programs that can assist you in this task. They will often conduct the survey for you, supply a detailed inventory list and show commonality of inventory parts for consideration.
Data is the key to unlock cost savings.
This detailed pump data, along with shop maintenance records, is key to determining where the biggest performance gains can be made. By reviewing shop records to see what was done the previous times a bad actor was repaired, you should be able to better determine whether a different solution is required. If changes are made to the pump equipment, they should also be noted in the pump data through ongoing remediation.
Footnotes
- “NPSH, NPSHr & NPSHa Definition,” Intro To Pumps, retrieved 20 October 2017 from https://www.introtopumps.com/pump-fundamentals/pump- terms/npsh-net-positive-suction-head-required-available/
- “NPSH – Calculating It,” McNally Institute, retrieved 20 October 2017 from http://www.mcnallyinstitute.com/11-html/11-12.html
- Robert X. Perez, Operator’s Guide to Centrifugal Pumps: What Every Reliability-Minded Operator Needs to Know, Volume 2, Xlibris, 16 February 2015, 31-34
- Heinz P. Block and Alan R. Budris, Pump User’s Handbook: Life Extension, The Fairmont Press, Inc., 2004, 321-326
- Scott Weston, “Why Remediation of CMMS Data is Essential to Reliability-Centered Maintenance,” retrieved 20 October 2017 from https://reliabilityweb.com/ articles/entry/why_remediation_of_cmms_data_is_essential_to_reliability-centered_maintenance.