API Regulation Seal Pot Pressure Vessels
Carotek.com displays pricing in accordance with our manufacturer’s internet pricing policies. Contact us for volume discounts and quotes.
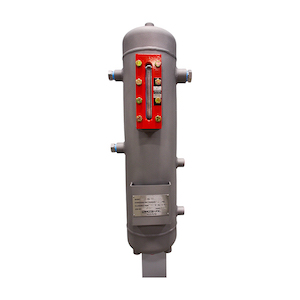
- Details
- Industry / Applications
- How Seal Pots Work
- Documents
API Regulation Seal Pot Features
Pressurized barrier fluid reservoir and circulation tank to ensure media will not leak into atmosphereDesigned to ASME Section VIII, Division 1 standardsAvailable to build to (U) and (UM) stamps, registered with national boardFormation of fluid between seal faces provide a longer seal lifeModular design for various combinations of instruments and components Available with refill pumps, transmitters, switches and cooling coils
Specifications
Tank Capacity: 2 Gallon, 3 Gallon, or 5 Gallon in 6" or 8" diameter Operating Pressure: 400 PSI @ 200°FTank Material: 316/316L SCH 40Cooling Coil: 1/2” x 0.065” wall seamless tube; 20’ long 316/316LLevel Gauge: Weld Pad– Size 7, 10 ¼” VisibilityHydrostatic Test Pressure: 525 PSIAllowable Temp: -20° F to 200° FFill Port: 3/4” NPTSeal Connections: 1/2” NPTLevel Switch Connections: 3/4” NPT
Options
Pressure Regulator specific to your applicationPressure Indicator 2 ½” Dial - Pressure specific to your applicationExplosion Proof Ultrasonic Level SwitchCode Stamp available either (U) or (UM)
ANSI Seal Pot Applications
Leak free seal service on chemical applicationsToxic FluidsEPA regulated fluidsExpensive fluidsHazardous fluids
Carotek manufactures Seal Pot Pressure Vessel Tanks in our Charlotte facility in Matthews, NC. The seal pots are built toASME Section VIII, Division 1, E2007, 2008a, Addenda and are available with ASME “U” and “UM” code stamps. As a premier industrial seal pot manufacturer, we offer standard and custom built ANSI / API mechanical seal support systems for industrial, chemical, and petrochemical applications. Seal pots provide a protective buffer between the product and the atmosphere, and isolate potential product leaks to the atmosphere. As a safety measure, seal pots perform a vital duty protecting the environment and personnel from the dangers of hazardous materials
Our Seal Pots our fully Made in America and meet all the requirements of ANSI and API specifications. Our modular designs are adaptable and can be combined with cooling coils, level switch/transmitters, pressure switch/transmitters, air coolers, and circulating pumps for a wide variety of applications. They are durable, flexible, and offer reliable performance for your demanding operations. Modular design supports various combinations of instruments and components such as built in refill pumps, transmitters, switches and cooling coils.
Why Buy Carotek Seal Pot Pressure Vessels?
Seal Pot ASME Certificate of AuthorizationMade in AmericaQuick QuotesQuick DeliveryExpert application assistanceMillwright qualityTIG and MIG weldedBare Tanks with coil can be shipped next dayAvailable with ASME code stamp
Leak free seal service on petrochemical and refinery applicationsToxic FluidsEpa regulated fluidsExpensive fluidsHazardous fluids
A non-pressurized external reservoir system acts as a protective buffer between the product and the atmosphere. Multiple seal arrangements are used to isolate toxic gases and fluids that can change state when exposed to the atmosphere. Buffer fluid is circulated between the inner and outer seal chamber using forced circulation with a circulating ring or pump.
Carotek also provides cooling coils to be placed in the seal reservoir to help reduce flashing of the product or the buffer fluid. A standard inner seal safely vents vapor to a recovery system so that zero emissions are achieved.
A pressurized external barrier fluid reservoir system supplies clean fluid to a pressurized dual mechanical seal with forced circulation. Pressurized barrier fluid is used to lubricate both the inner and outer seal faces. Maintaining the barrier fluid at pressure 25 to 30 psi above the seal chamber pressure insures barrier lubrication of the inboard seal faces.
Quote Specifications Form
Selection Guide