You can reduce the impact of longer lead times in process equipment by following some of Carotek’s tips based on best practices. These techniques are often used in supply chain management for companies selling product, but can also be applied to making sure you have the process equipment and parts you need to keep your facilities running.
We know lead times have become a real issue during the Covid Pandemic. We are doing everything we can at Carotek to help. We can’t guarantee we will always have the product you need, but we will work with you to find a solution.
According to Stephen Bell, President - Carotek, "Manufacturers and distributors are experiencing backlogs as much as 50% above the average of 2015 – 2019. As manufacturers increase production to catch up, we expect to see the backlogs come down to more normal levels. However it could be the end of Q2 before these backlogs begin to level off."
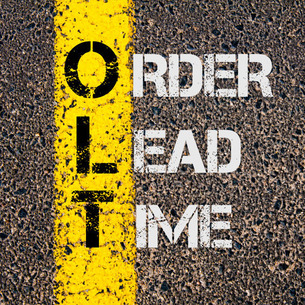
Importance of Lead Time in Process Equipment
Long lead times on process equipment can be detrimental for your business because they may mean that your production line experiences increased downtime. There are a number of things you can do to help minimize any production downtime due to the delays on delivery of process equipment and parts.
6 Lead Time Reduction Methods
“Carotek is here to work with your MRO or project needs and can assist you in developing a plan for critical spares, long-lead items, and alternate products/solutions” says Dave Webster, VP Sales - Process Automation.
These six techniques will help to ensure you have the pumps, valves, instrumentation you need to optimize your production.
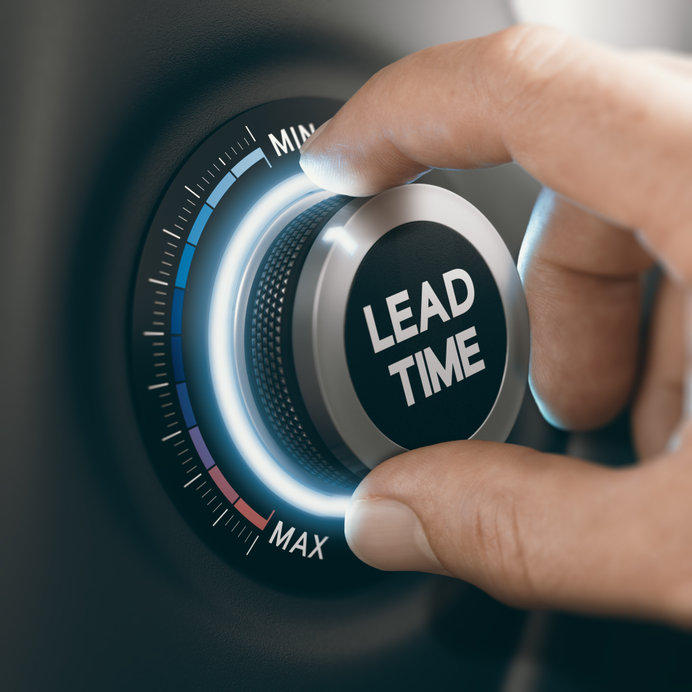
1. Source from an Authorized Stocking Distributor for your location
Having your orders fulfilled by a local supplier could cut your lead times by weeks. Authorized distributors are held to certain inventory standards and because we know the region’s manufacturing businesses, we can forecast and stock the items most most frequently purchased by customers.
2. Plan your Maintenance and Stock Important Parts
The best way to plan your maintenance in advance is for us to do an equipment and parts audit. We will come on-site, make a list of your process equipment and recommend the parts you should have on hand, as well as a regular maintenance schedule. You’ll get a detailed list of your assets with IOM’s, parts BOM’s, part numbers and pricing. We will list common models to let you know what common parts you can stock to cover multiple assetts.
Many suppliers offer part “kits”, so you have everything you need in one box to perform repairs and service. These part kids are easier to stock and easier to install. Carotek also offers a contracted service to stock parts for you – which keeps your budget in check without compromising your access to parts that you need.
3. Prompt Communication
When an unplanned need for process equipment occurs, make sure that you reach out to our office immediately so we can check inventory and/or get an order placed. Many of our authorized distributor products have online inventory portals where we can see and share inventory with up to 45 other distributors across the nation. We can also offer expedited shipping options as desired.

4. Plan Ahead for System Upgrades
Don’t underestimate the importance of planning ahead for production line equipment enhancements or changes. Remember, we are here to help with that planning. Our expert solutions consultants can contribute to your project planning to help avoid any unnecessary delays due to equipment availability. We know which manufacturers are having delivery issues and how to propose different solutions.
Get in touch with us in the planning stage of your projects so we can tell you the average lead times for typical long lead custom packaged equipment. You may need to order earlier than in the past due to increased backlogs manufacturers are presently experiencing.
5. Order Less, More Often
Large orders usually take suppliers longer to prepare and ship, which obviously increases your lead time if products are arriving later. Ordering more frequently but in smaller quantities reduces your risk of late shipments. Don’t wait – order now. If there are significant shipping savings, we can hold your products until they all arrive and ship together.
6. Share Forecast Reports
Make sure Carotek is up-to-date with your demand forecast for equipment and parts. This way we can help prevent lead time delays and system downtime. If you have usage reports you can share Carotek can offer to stock items specifically for your critical equipment to maintain uptime.
Managing your process equipment sourcing and maintenance schedules can positively impact your facility’s processing uptimes and increase your production output. Contact Carotek for assistance. We will do everything we can to help you.
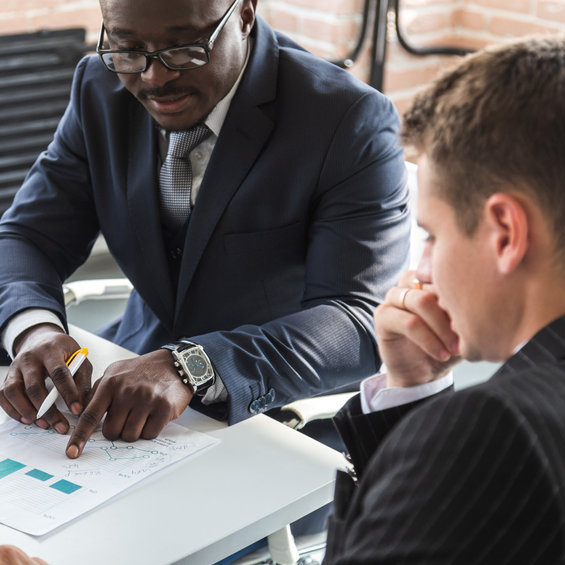
Get Help with Lead Times