Featured Pump Articles
- Turkey Processing Plant Saves $50,000 Annually and Reduces Energy Consumption by 50% with a High - Pressure Washdown and Sanitation System
- Save up to 50% Energy by Optimizing Pumps
- BioGill Wastewater Treatment for Food & Beverage Industry
-
Grundfos Food & Beverage Process Water Case Studies and Product Features
- AODD Pumps and Diaphragms for Food & Beverage Applications
- Are You Using Counterfeit Pirated AODD Pump Parts ?
- Industrial Blower Service Maintenance
- Guide: How to Prevent and Fix Leaking Pump Seals
- Wilden AODD Pumps Outperform ARO, Yamada, Graco, Sandpiper, Versamatic and Murzan
- Centrifugal Pump Training in Minutes by Griswold
- Hemp Market Proven! Ethanol Extraction CBD Oil Pumps
- Carotek solves customer's leaky seal and pump cavitation problem
- Gear Pump Troubleshooting Checklist and Videos
- Case Study: Plant Solved Shaft Breaks in Positive Displacement Gear Pumps?
- Request a FREE Pump Site Survey ($2500 value)
- How To Set Up a Pump Reliability Program - Do You Know When Your Pumps Will Fail Next?
- Tips to Improve Your Pump Uptime
Grundfos Food & Beverage Process Water Case Studies and Product Features
December 21, 2022
The food and beverage industry is in the middle of a transformation driven by the need for more sustainable, efficient, and digital manufacturing.
With Carotek and Grundfos, there’s already a way to reach these goals together. We partner with our customers across dairies, soft drinks, breweries, and food processing to optimize their facilities process water usage by applying the full potential of intelligent solutions. Every day, we are driving towards more sustainable, efficient, and smarter food and beverage production – without compromising the safety and quality that our world relies on.
Learn more from our hand picked white papers, case studies and product features.
White Paper - Harvest The Full Potential Of Water Reuse For Your Business
Intelligent solutions can help industries across the globe to treat and reuse their water in production and manufacturing, thereby minimizing water consumption and reducing their environmental footprint.
Water demand by food and beverage manufacturers is expected to increase 400% by 2050, making water a critical resource. With Grundfos, companies can reduce their environmental footprint by recycling up to 80% of their industrial wastewater with a water reuse system.
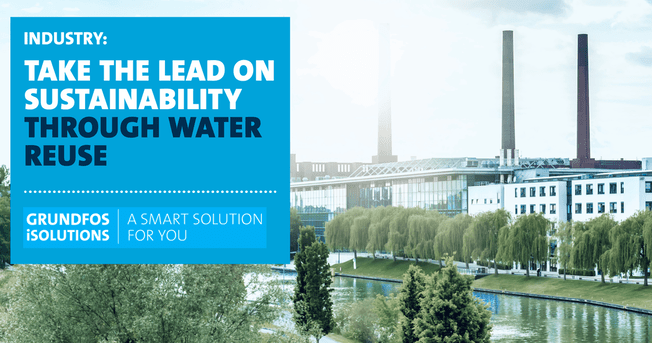
Case Study - Carlsberg Brewery Reuses 90% of its Process Water
Carlsberg brewery wanted to cut its water use by 50% by 2030. The initiative, Zero Water Waste, is part of Carlsberg’s Together Towards Zero program. In its production facility in Fredericia, Denmark, Carlsberg has developed a Total Water Management treatment plant with consultants, universities, and technology providers like Grundfos.
The onsite facility treats used process water from mainly cleaning purposes, purifies it to drinking water quality and sends it back to the brewery to be reused as process water. The plant now recovers and reuses 90% of its process water.
Case Study - Production Capacity Growth and Water Pretreatment Requirements
MadTree Brewing, Ohio’s first canned craft brewer has used reverse osmosis (RO) for all its process water. Reverse osmosis can customize the water source, a critical process in producing MadTree’s critically acclaimed portfolio of beers.
One of the biggest challenges is keeping up with demand. After hitting a maximum capacity of 25,000 barrels of beer, the decision was made to relocate to a new, expanded location. By adding the potential capacity to support future growth, output could be boosted to 180,000 barrels. They also had a new set of municipal requirements for pretreatment, which involved a chemical injection in the pre-filter section of the RO unit to eliminate chloramines used in the city water.
Find out how they solved these challenges.
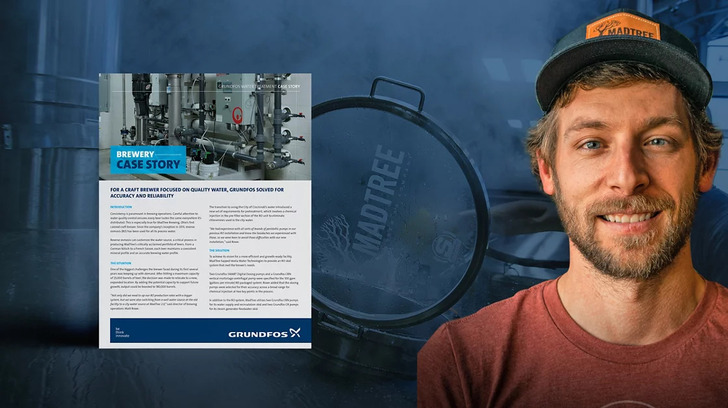
Case Study - Safe Foods installs Grundfos Smart Dosing Pump
Safety and consistency are essential when supplying food to 250 million people each day. To solve the challenges Safe Foods was facing when dosing peracetic acid, the company partnered with Grundfos to develop a solution by leveraging the Grundfos SMART Digital dosing pump. Variable speed stepper motors in chemical feed pumps open the door for smart technologies.
Grundfos’ smart drive strategies like AutoDeaeration, AutoFlowAdapt and always using 100% stroke length allow for accurate, smooth and continuous dosing that results in safe and reliable chemical delivery every time. Each SMART Digital dosing pump is not only safe and accurate, but it can pinpoint exactly where an issue occurs—allowing Safe Foods’ customers to monitor what’s happening in real-time, identify when it happened and keep the events in their records.
The food processing plants benefit from less downtime, fewer maintenance calls and lower chemical costs. Through this partnership, Safe Foods continues to ensure a safer food supply for the world.
Intelligent dosing pumps are the ideal solution for any kinds of complex dosing in less aggressive environments. Offering a high level of accuracy, digital dosing pumps not only reduce the chemical waste, but also the energy bill.
White paper - Replacing Old High Pressure Pumps with New Technology for a Cost-Effective Pumping System
High-pressure washdown systems are vital to food processing plants, but inefficient operation and costly maintenance shouldn’t have to be. Finally, there’s a better way to run your washdown system using new technologies.
Grundfos Hydro HP High pressure Washdown System offers full ROI in just a few maintenance cycles. The cleaning and washdown systems in most food processing facilities run on pitot tube pumps that use too much energy with inefficient performance. The Grundfos Hydro HP solves these old problems with the superior hydraulic performance of CR/CRE pumps.
Hydro HP is a fully integrated high-pressure booster system offering a more reliable and energy-efficient solution for clean and wash applications. The system features industry-leading CR vertical multistage inline pumps, which offer superior hydraulic performance and bulletproof reliability in a space-saving footprint while the integrated VFD control offers consistent system pressure.
Complete, Efficient Solutions to meet Processing Plant Demands
Managing a plant means optimizing processes, maximizing uptime, managing resources, and ensuring the safety of workers and products to meet government regulations. With Grundfos, you gain more than a pump supplier, you gain a partner focused on solving the challenges of your operation and delivering higher efficiency and reliability than you thought possible.
Dedicated to innovation and a pioneer in water technology, Grundfos continuously advances our products and capabilities to meet the increasing need for connectivity, accuracy, and efficiency in our ever-evolving industry.
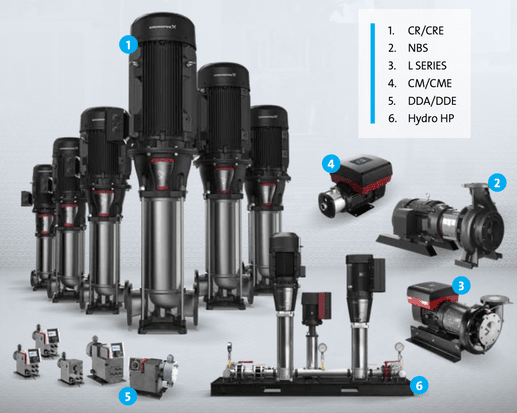