Featured Instrumentation Articles
- Watlow Process Heating Resources Downloads
-
Case Study - Chemical Plant saves 200K with Endress+Hauser Memograph
- Endress+Hauser Shows How Production Data can Increase Efficiency and Output
- Should I Use Diaphragm Seals or Isolation Rings to Protect Plant Instrumentation from Harsh Process Fluid?
- Endress+Hauser Feature: Micropilot Radar Level Measurement
- Reduce Energy Use with Industrial Process System Energy Savings Audits
- Endress+Hauser Featured Downloads – Q4 2022
- Eurotherm Process Control Instruments for Food & Beverage Industry
- Armstrong Food & Beverage Products & Services
- Endress+Hauser Instrumentation Meet Food & Beverage Demands for Stringent Measurement
- Armstrong International 2022 Innovations
- Endress+Hauser Featured Downloads – Q3 2022
- Detect Gas Leaks Quickly in your Facilities
- Prevent Dust Explosions at your Plant
- Solve Institutional Hot Water Requirements: Prevent Legionella and Water-Borne Pathogens
- Water/Wastewater Systems Problems Guide
- Grundfos Commercial HVAC Guide - Summer 2020
- What Carotek offers Commercial and Institutional Plumbing
- What are the Four Classic Energy Measurements in Water (Head) ?
- How to Know Why and When do your Flowmeters need Calibration?
Case Study - Chemical Plant saves 200K with Endress+Hauser Memograph
Goulston saves 200K by implementing Advanced Data Manager Memograph RSG45 technology
Solution offers reliability and cost savings to a chemical plant
Benefits at a glance
- Process optimization
- Cost savings
- Increased efficiency
- Better overall functionality
- Ease of installation and maintanence
- Increased personnel safety
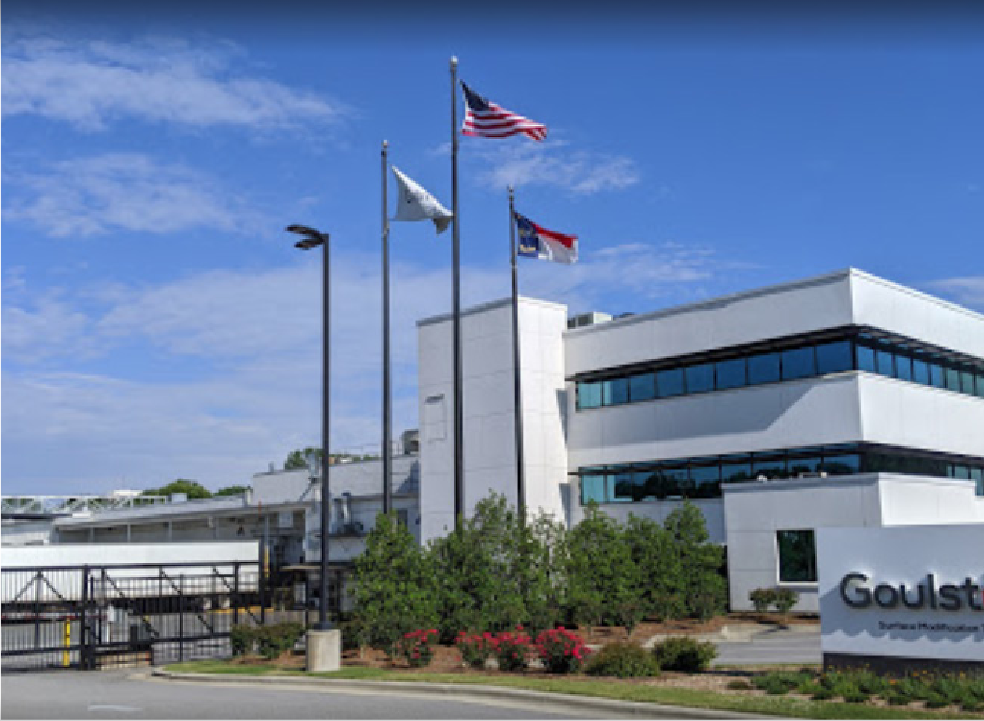
Summary: Located in Monroe, North Carolina, Goulston Technologies, Inc. is a leading provider of surface modification technologies for fiber lubricant products in the chemical industry, offering its technologies and services to customers in more than 40 countries
To produce top-quality innovations and technologies within the surface modification industry, it is important Goulston’s processes run as accurately and efficiently as possible. However, when previously used technologies resulted in added time and money being put into a process, it was crucial these issues be met with timely solutions. This is exactly the challenge Goulston faced when looking to optimize the batch chemical process in its tanks as the company wanted to concentrate all its data into one system. Current supply chain issues for PLC I/O input cards posed a serious challenge, until Endress+Hauser’s Advanced Data Manager, the Memograph M RSG45, was introduced as an alternative to the company’s current data management system. This solution allowed Goulston to cut back significantly on input cards and wiring while still maintaining accurate and reliable data recordings.
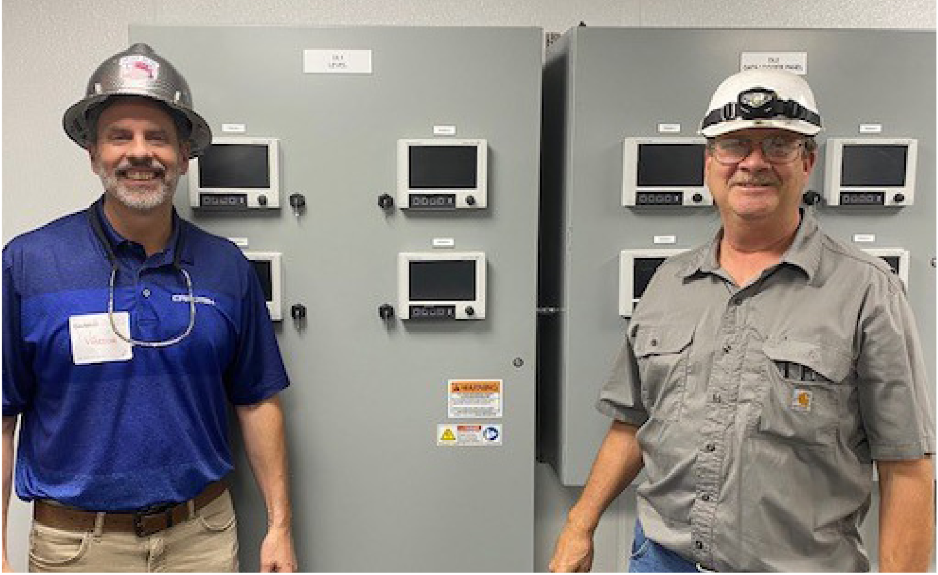
Challenge: Before installing the Advanced Data Managers, Goulston had planned to add more I/O cards to their PLC for data management of various applications. The company experienced supply chain issues related to these cards, which sent them looking for alternative options. Goulston also had a desire to limit the number of wires to their PLC and wanted to include EtherNet/IP™ communication so that they could ease access and consolidate inputs from the field back to the PLC.
With the high number of individual instruments in the field, wiring and cabling became a challenge. The current method of having each instrument connected to the PLC with a dedicated input added additional complexity and cost.
Without the RSG45 panels, we would have had to order more than 140 additional analog input cards, that we actually can’t get delivered right now,” said Tyler Hurst, instrumentation engineer at Goulston. “This would have put our project behind schedule and would have created a mess of cables and wires since there would have been multiple racks and extra PLC panels.
Our Solution: Kyle Bernhardt, at Carotek, Endress+Hauser’s sales and service partner, has been supporting and collaborating with Goulston’s Tyler Hurst for 10 years. Over the years, Kyle has been able to provide and share innovative solutions with the company. When Tyler brought the challenge to the Carotek team, the Advanced Data Manager was a solution brought to the table. Using Carotek’s expertise and UL approved panel shop, 14 data managers were installed, wired and tested within four different panels. This gave Goulston the solution they were looking for.
The Advanced Data Manager adapts quickly and easily to any application and the measured values can be easily transferred to plant modules that can be interconnected. The device can receive up to 20 inputs which would allow various instruments to provide measurements simultaneously. This reduces the number of PLC inputs previously needed along with the amount of cables and wiring. These data managers would integrate into Goulston’s current control system via EtherNet/IP communication. They also serve as a gateway providing control, data access and convenient configurations to the instruments in the field. The remote capability allows for both ease of access and increased safety for plant personnel.
Carotek not only provided Goulston with 150 instruments, including flow, pressure, level and temperature devices, but they were also able to pre-program the Advanced Data Managers and customize each individual input. Completely wired panels would enable the customer to finalize installation with ease.
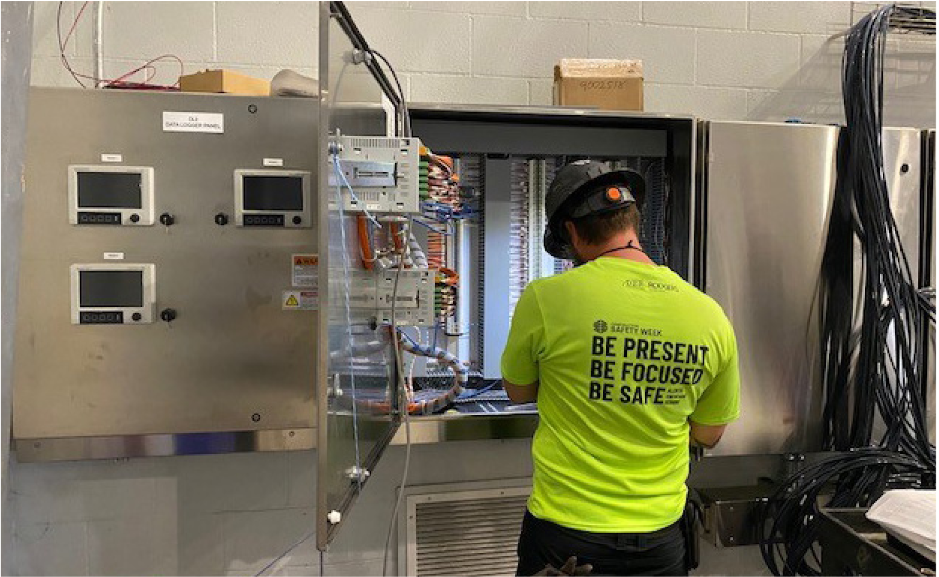
Results: Previously, Goulston would have needed to buy individual I/O cards for each instrument that they had in their process. This meant spending thousands of dollars on parts and wires to ensure accurate readings. By implementing the Advanced Data Managers, they were able to cut the number of input cards by 140. By doing this, Goulston was able to save approximately $150–200k.
“In a nutshell, these panels more than paid for themselves just with the cost of the modules, extra cost of wiring, cost of additional panels and everything else this removed,” added Hurst. “None of this even gets into the EtherNet/IP and control system connectivity value the Advanced Data Manager provides. We have already seen this value on the panels for our tank level that we tested them out on.”
With the increased cost savings, efficiency and overall functionality the Advanced Data Manager offers, Goulston will be able to put more time and resources toward ensuring the high quality of the product they provide for their customers.
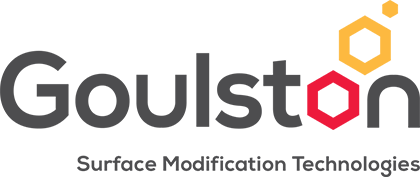
With more than 75 years of industry experience, Goulston is a market leader in the chemicals sector. While much of our experience and history is in the synthetic fibers area, we also have developed expertise in other surface modification technologies. Our mission at Goulston is to be the global leader in surface modification technologies by providing our customers with innovative products and services that are consistently superior in technology, quality, performance and value
About Goulston